===============================
아래의 글은 2010년 하버드 비즈니스 리뷰 (일본어판)에서 나온 글을 2차례에 나누어 번역 소개한다.
글을 적은 사람은 골드렛("더 골"이란 책을 지었고, TOC라는 이론 제시한 박사)이다. 오노 다이이치를 추모하면서 적은 글이다.
================
포드로부터 배워 포드를 능가한 사람, 오노 다이이치 1
출처: 하버드 비즈니스 리뷰 (일본어판) 2010년 1월
- Eliyahu M. Goldratt (골드렛)
제조업은 헨리 포드와 오노 다이이치라는 두 사람의 위대한 사상가에 의해 형성되었다. 포드는 흐름작업 방식의 도입에 의해 대량생산에 혁명을 일으켰다. 한편 오노는 도요타 생산방식을 중심으로 포드의 아이디어를 한층 발전시켜, 재고는 자산이 아니라 부채라는 생각을 이끌어 냈다.
오노의 위업을 이해하는 데에는 먼저 포드의 업적에 대해서 알아들 필요가 있다.
헨리 포드의 발명
운영(Operation)을 통해 제품 생산을 하는 과정 전체의 흐름을 부드럽게 하는 것이 낭비없는생산을 하기 위한 열쇠이다. 이것이 포드의 출발점이었다. 그래서 포드는 "흐름' 의 개선에 노력했고, 이것은 대성공을 거두었다. 철광석을 채굴한 후, 5,000점 이상의 부품을 조립하여 완성차를 만들어,이를 수송하는 열차에 적재하기까지의 리드타임(Lead Time)이 1926년에 81시간으로까지 단축시켰다.
흐름이란 오퍼레이션 내의 재고가 움직이고 있는 것을 의미한다. 재고가 움직이지 않으면 재고는쌓인다. 재고가 쌓이면 장소를 차지한다. 이 때 직감적으로 떠 오르는 해결책은 재고가 쌓이는 공간(space)를 제한하여 흐름을 개선하는 방법이다.
포드는 작업현장(공정)과 작업현장(공정) 사이에 재공품을 두는 공간에 제한을 가했다. 이것이 흐름 작업방식의 본질이다. 최초의 흐름 작업방식에서는 재고를 작업현장(공정)에서 다음 작업현장(공정)으로 이동시 벨트 컨베이어와 같은 기계를 이용하지 않았다는 점으로도 잘 알 수 있다.
포드의 흐름 작업방식이 얼마나 놀랄만한 것인가는 공간에 제한을 설정하여 생겨난 결과를 통해 잘 알 수 있다. 만일 그 공간이 재고로 가득 쌓이게 되면 작업자가 생산을 멈출 수 밖에 없었다. 결국 흐름을 부드럽게 하기 위해 포드는 부문효율을 희생할 수 밖에 없었다. 바꿔 말하면, 흐름작업방식은 모든 작업자와 작업현장이 100% 바쁘게 가동하지 않으면 안 된다고 하는 상식을 무시하는 것이었다.
다시 말하면, 쉼 없이 자원을 사용하여 가동시키지 않으면 생산 오퍼레이션이 떨어져 쓰루풋 (Throughput)이 낮아진다고 생각할지 모른다. 만약 포드가 공간의 제한에 만족했더라면 그와 같은 그와 같은 바람직하지 않은 결과가 초래되었을 것이다.
그러나, 재고가 일정한 수 이상 쌓이지 않도록 제한하는 것에는 다른 효과도 있다. 그것은 본래의 문제, 즉 즉, "흐름을 나쁘게 하는 것은 무엇인가?" 를 가시화하는 것이다. 결국, 라인상의 어느 작업현장이 짧은 순간 생산을 멈추면 즉시 라인 전체가 즉시 멈춘다.
포드는 "라인이 정지해 있다"는 가시화된 상황을 공장의 생산능력 (capacity)이 아니라 흐름의 균형 (balance)이란 관점에서 대처해 나갔다. 이런 활동을 통해 부문적인 효율을 회생하고 흐름을 균형 있게 하여 쓰루뜻 (Throughput) 을 대폭 향상시켰다. 포드는 작업자 한 명당 쓰루풋(Throughput)에 있어서 당시의 자동차 메이커 중 최고 높은 수치를 실현하였다.
오노 다이이치의 도전
오노의 목표도 포드와 같이 흐름을 개선하는 것이었다. 다시 말하면, 리드타임을 단축하는 것이었다. 이를 위해 "도요타는 어떤 일을 하였는가?" 라는 질문에 그는 "고객의 주문하고 난 뒤 우리가 대금을 회수할 때까지의 시계열을 보고 있다.” 라고 답하였다.
간반방식을 발명하다
오노는 과잉생산을 막기 위한 개선에 함하였을 때 커다란 장애에 직면했다. 어떤 제품에 대한 수요가 확대될 때에는 포드가 했던 것처럼, 각 부품을 생산하기 위해서 어떤 라인을 그것만을 만들 수 있도록 전용화하는 것이 정당화된다. 그러나, 당시 일본 자동차시장에서는 다품종 소량생산이 요구되고 있었기 때문에 도요타는 라인을 전용화할 수 없었다.
이와 같은 상황에 직면했음에도 불구하고 업계 대부분은 '복수의 라인 사용' 에 대해서 심도있게 생각하지 않았다. 그러나 오노는 장치를 전용화할 수 없음에도, 개개의 작업현장이 여러 가지 부품을 생산하기 위해서 복수의 라인 사용이라는 아이디어에 대해 여러가지 궁리를 했다.
문제는 공간에 제한을 설정하면 라인이 마비돼 버린다는 점이었다. 즉, 공정간의 공간이 가득 차게 되면(공급라인의 작업이 멈춤), 조립용의 부품 모두가 사용되지 않는다 (조립 작업이 정지함)
오노는 슈퍼마켓에 관한 이야기를 들었을 (그가 1956년에 미국을 방문, 슈퍼마켓을 실제로 눈으로 보기 전의 이야기임), 갑자기 해결책이 떠올랐다고 회상하고 있다.
슈퍼마켓에서는 상품이 판매되면 그 양만큼을 보충한다. 결국 필요한 수의 재고를 정확한 타이밍에 다음 공정에 흘리면 라인이 마비되는 일이 없어진다. 즉 흐름이 균형 있게 된다고 생각한 것이다.
오노는 언제 생산하지 않아야 하는가를 구현할 수 있는 오퍼레이션 시스템에 대해서 생각했다. 그는 포드의 방법을 뛰어 넘어 개개의 부품이 쌓이는 양을 제한하려고 했다. 이를 위해로 생겨난 것이 소위 '간반방식" 이다.
간반방식은 "무엇을 언제 생산할 것인가?" 뿐이 아니라 그 이상의 중요한 "언제 생산하지 않을
것인가?"까지 알려준다. 결국, 과잉생산을 막는 도구이다. 이와 같이 오노는 언제 생산하지 않는가를 알리는 구조를 공간에서 재고로 변화시켰다. 오노는 이와 같은 포드의 생각을 계승 발전시켜 성공하였다.
기종교체시간을 단축하다
언제 생산하지 많는가를 알리는 간반방식을 현장에 도입하자면 쓰루풋(Throughput)이 일시적으로 떨어지기 때문에 흐름을 균형되도록 만드는 것이 새롭게 필요하게 된다.
오노가 직면했던 문제는 포드가 직면했던 것보다 훨씬 크고 곤란한 것이었다. 무엇보다 라인이 전용화되지 않기 때문에 어떤 제품에서 다른 제품으로의 빈번한 기종 교체를 모색 하지 않으면 안 되었다.
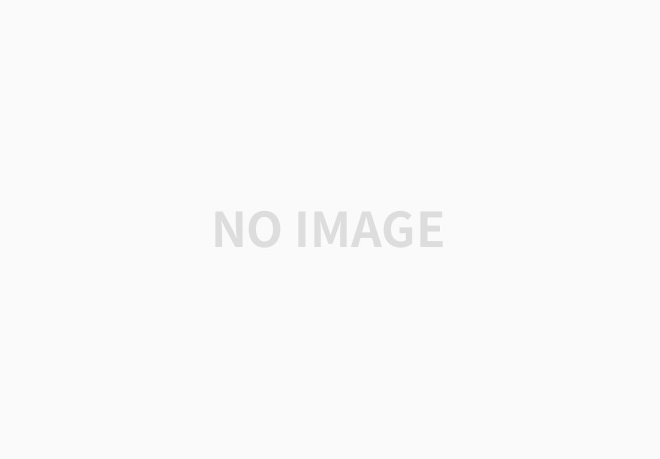
'제조업과 산업의 이해' 카테고리의 다른 글
(일본) 스마트 팩토리 사례. 일본 다이킨(세계 제일 에어컨 회사) (0) | 2019.10.26 |
---|---|
과학과 공학 연구 (일본인 노벨 화학상 수상자 요시나 인터뷰에서) (0) | 2019.10.09 |
one piece flow(한개씩 흐름 생산) and batch 생산(배치생산) (0) | 2019.10.03 |
설계능력이 부가가치 (0) | 2019.07.23 |
이용가능률(availability, 가동도) 가동률(可動率)과 가동률(可動率) 차이 (0) | 2018.07.09 |